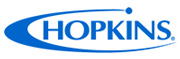
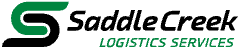
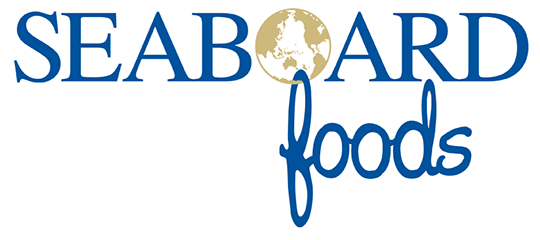
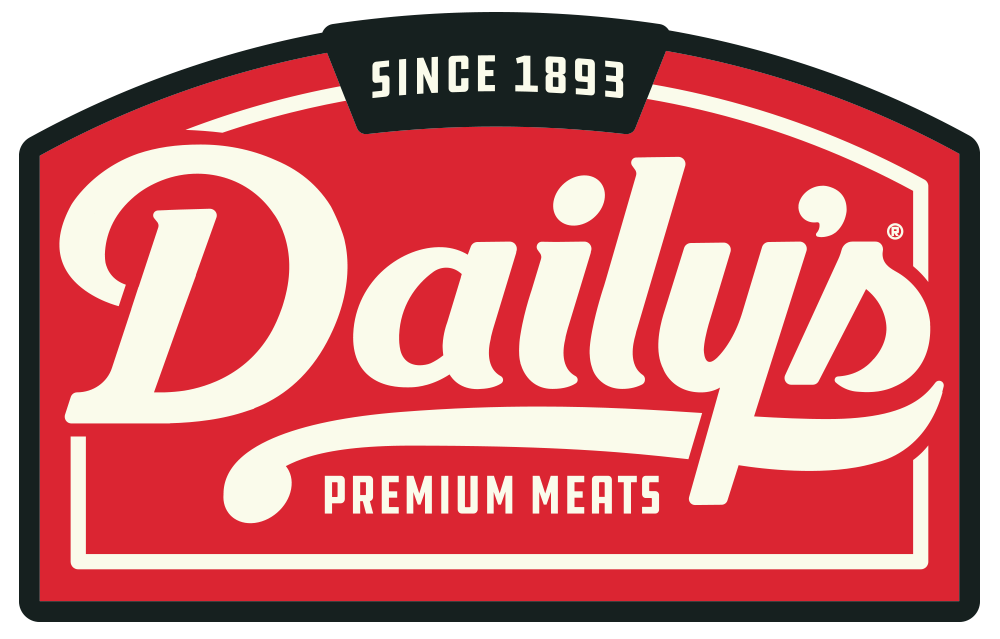
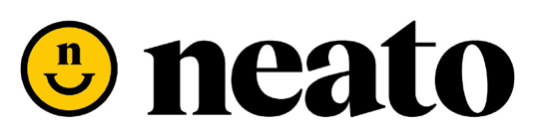
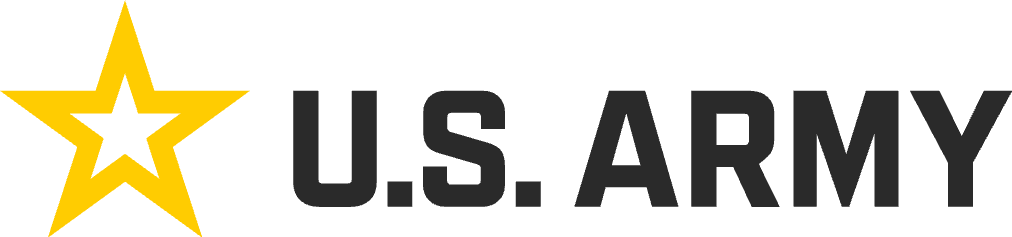
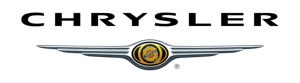
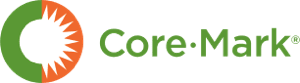
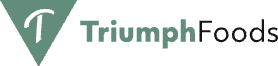
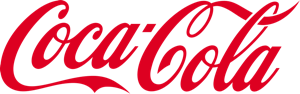
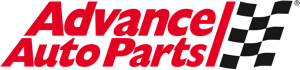

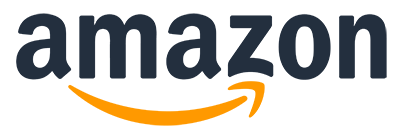
Recognition
at Every Level
$$$$
Millions Saved
With top-tier expertise, we bring a track record
of "Best in Class" results to every partnership
About
Hammer Legacy, is a results-driven consulting agency specializing in supply chain and distribution center operations, driven by Lean Six Sigma Continuous Improvement Methodologies & a commitment to Operational Excellence. We bring extensive experience and expertise in optimizing Supply Chain & Distribution Center Operations across various industries. Our team of seasoned professionals combines in-depth knowledge of Lean Six Sigma principles with a relentless pursuit of Continuous Improvement to drive tangible bottom-line results for our clients. With a deep understanding of the challenges faced by modern businesses in the dynamic landscape of Supply Chain Management, we offer tailored solutions that streamline processes, eliminate waste, and enhance overall operational efficiency. Our approach is rooted in Lean Six Sigma, a proven methodology that focuses on reducing variability, improving quality, and maximizing value creation.
Services
& 4PL SERVICES
Achieve logistics excellence with our 3PL and 4PL services, anchored in Lean Six Sigma and relentless optimization. Partner with us for unmatched efficiency and success, setting new standards in supply chain management.
Optimization
Our consultants optimize supply chains with Lean Six Sigma, specializing in network design, site selection, and tech upgrades. We ensure smooth transitions and sustained improvements through Change Management.
Center Consulting
Our Lean Six Sigma fortified logistics expertise optimizes warehouse efficiency, space, and operational flow. From automation to outsourcing, we tailor solutions for Continuous Improvement and industry-standard redefinition.
(Fulfillment by Amazon)
Consulting
Elevate operations with our Implementation services, driving efficiency and quality through comprehensive programs and protocols. Utilizing DMAIC methodology, we guide you through challenges with clear benchmarks and KPIs.
& GLOBAL OPERATIONS
We pioneer proactive crisis aid and security strategies, leveraging logistics and humanitarian expertise. Our mission is to empower communities to withstand adversity and thrive through swift distribution and holistic solutions.
Our approach = systematic & disciplined
Unlock the full potential of your Supply Chain & Distribution Center Operations with Hammer Legacy. Our Data-Driven & Fact Based approach, rooted in Lean Six Sigma Methodologies, drives Continuous Improvement & Operational Excellence. From thorough assessments to customized solutions and seamless implementation, we empower businesses to optimize processes, reduce waste, and enhance efficiency. Partner with us to transform your operations, achieve measurable results, and stay ahead in today’s competitive landscape.
Continuous improvement is a journey,
you just need the right guide…
The first step in your journey to Continuous Improvement starts with you. You simply have to decide on taking the first step. We offer tailored solutions to optimize your Supply Chain & Distribution Center Operations. Whether a comprehensive transformation or a streamlined implementation, our flexible approach caters to projects of all scopes & sizes. Experience exceptional results, enhanced efficiency, & sustainable growth with our proven expertise in driving Operational Excellence.
Real World Experience
-
Stellar Transformation: Turning the Tables for Distribution Center Operations
Company: Coca-Cola Refreshments
Backdrop:
The Distribution Center (DC) at Coca-Cola Refreshments grappled with a myriad of hurdles in optimizing their distribution operations, spanning warehouse to direct store delivery teams. Fueled by a relentless pursuit of operational excellence, they embarked on a groundbreaking continuous improvement expedition. Their goal was to revamp efficiency, elevate service levels, and secure extraordinary outcomes via the potent implementation of Lean Six Sigma initiatives.
Pain Points:
Dismal Market Unit Ranking: The distribution center found itself anchored at the bottom in critical metrics within its Market Unit and unmentionably low within the company’s operations network. The stark data indicated an undeniable need for both operational transformation and cultural upheaval.
Operational Inefficiency and Layout Constraints: An ill-conceived warehouse design and layout stifled productivity, leading to operational bottlenecks, poor inventory management, and safety risks.
Deficient Onboarding and Development Programs: The lack of a holistic onboarding and developmental training program obstructed employee assimilation and growth, resulting in a faltering corporate culture, characterized by disengaged leadership, lack of transparency, minimal ownership, and ineffective communication.
Service Level Deficiencies: The DC suffered from service level gaps due to an absence of accountability and process control, leading to undesirable outcomes throughout the Supply Chain Operation. Empirical data analysis underpinned the need for a Lean Six Sigma Operational Excellence program.
Strategic Solutions:
Warehouse Design / Layout Optimization: Spearheaded a comprehensive warehouse design overhaul, including SKU velocity, traffic flow analysis, innovative 5S program implementation (celebrated as Best in Class), and enforcement of process standards and controls. These improvement initiatives bolstered operational efficiency, laying a solid foundation for a culture of operational excellence.
Comprehensive Onboarding and Training Development Program: In alliance with the Human Resources team, a robust onboarding and cross-training program was implemented, (celebrated as Best in Class). This initiative streamlined the onboarding process and established a first ever learning center, ensuring all team members received effective, value-added training. This facilitated seamless integration, improved performance, and created career development opportunities, thereby fortifying the company’s talent pool.
Process Standardization and Expedited Delivery Implementation: Conducted a current state assessment and gap analysis, formulated a change and project management timeline to level set key stakeholder expectations. This included establishing standard work documentation (sop’s, policies, forms, work instructions, etc…) benchmarking, process evaluations / audits and project milestones. We spearheaded the implementation of a new rapid delivery solution resulting in significant improvement for both direct store delivery and driver safety. Through new process standards and controls, the distribution center excelled, exceeding expectations, and enhancing customer satisfaction.
Process Control & Accountability Program: Aligned with the company’s mission, values, and strategic vision. We took ownership of the designing, training, and implementation of the overall program. We provided pivotal support so the company could gain control and sustain the overall success of the change management project for both near and long-term goals.
Breakthrough Results:
Operational Metamorphosis: A stunning turnaround saw the DC skyrocket from the last position in its Market Unit to a commendable #3 companywide ranking within just 18 months. Eventually, it secured the top spot in the network, showcasing the transformative potential of Lean Six Sigma in practical applications.
Reduced Costs, Boosted Efficiency and Service Levels: Labor costs dipped by 11.8% in direct store delivery operations and 37.8% in warehouse operations. Realized a 16.7% improvement in throughput. Service levels saw a remarkable enhancement with a 12.3% increase in OTIF (On Time In Full), 47.5% reduction in out-of-stock instances and a 33.8% improvement in order picking accuracy, thereby ensuring prompt and precise delivery to customers.
Recognition and Leadership Evolution:
The remarkable triumphs of the distribution center were mirrored in their skyrocketing rankings. They secured the apex position across the entire North American Field Operations group, within both total field operations (direct store delivery) and warehouse operations. This recognition illuminated the profound impact of Lean Six Sigma and a steadfast dedication to operational excellence. The Senior Vice President of North American Field Operations lauded the DC as “a showcase” and “Best in Class”. The successful integration of an Operational Excellence Culture, rooted in Lean Six Sigma, pushed the DC operations beyond expectations, and those involved saw their efforts rewarded with multiple career advancement opportunities.
Impressive Outcome:
Thanks to the diligent application of Lean Six Sigma methodologies and a robust commitment to continuous improvement, the distribution center underwent a phenomenal transformation. Their journey from being a laggard to achieving a “Best in Class” status, underscored the tangible benefits of a relentless commitment to perfection through Lean Six Sigma. By revamping and standardizing all facets of operation and executing a comprehensive onboarding and training program, they realized substantial gains in efficiency, service quality, and financial performance. This success story stands as a testament to the potency of Lean Six Sigma in overcoming challenges and delivering spectacular results.
Endnote:
Continuous Improvement is a Journey, You Just Need the Right Guide…
-
Empowering Change: From a real life ‘Living Hell’ to Top 5
Company: Core-Mark International
Backdrop:
The Atlanta Division faced inefficiencies and outdated processes and was literally described as a “living hell.” Ranking dead last, 27 out of 27 Divisions. The operation was the running “joke” of the Company. To overcome these challenges and strive for operational excellence, the organization embarked on a transformation journey. By leveraging Lean Six Sigma methodologies, change management, and project management initiatives, significant improvements were achieved across multiple areas.
Pain Points:
- Subpar operational efficiency demanded an intensive operational overhaul.
- High Overtime and Shrink: Excessive overtime and significant shrink indicated the need for enhanced productivity and inventory management.
- Inadequate Policies and Guidelines: Insufficient policies and guidelines for employee evaluations, recruitment, and promotion hindered productivity, safety, and morale.
- Non-Compliant Safety Standards: Failure to meet required OSHA safety standards highlighted the importance of implementing a comprehensive safety program.
Strategic Solutions:
- Developed and implemented organizational policies, goals, and guidelines.
- Collaborated with Human Resources to create training and incentive programs for improved safety, productivity, and morale.
- Established an incentive-based program focused on key metrics and the company mission.
- Recognized and rewarded employees for their contributions to safety, throughput, operational excellence, and on-time delivery.
- Implemented a division-wide safety program to ensure compliance with OSHA and company safety standards.
- Addressed safety requirements for warehousing, transportation, and facilities. Operational Excellence Initiative:
- Developed and implemented short-term and long-term plans to drive Lean Six Sigma initiatives across management and the organization.
Breakthrough Results:
- Reduced overtime by 48.1% and shrink by 78.3%, significantly improving operational efficiency.
- Achieved a 39.1% improvement in Lost Time Incident Rate (LTIR) and a 32.9% improvement in Recordable Incident Rate (RIR). Service and Productivity Enhancements:
- Realized a 77.8% improvement in order accuracy and a 28.2% increase in on-time delivery.
- Boosted productivity by 12.1%, enhancing overall operational efficiency and customer satisfaction. Recognition and Leadership Evolution:
- Successfully implemented Lean Six Sigma and safety compliance initiatives.
- Offered employees career growth opportunities through the Associate Recognition Program.
- Overall Rank = #5 (out of 29 Divisions) in 1.5 Years
Impressive Outcome:
Through the dedicated application of Lean Six Sigma methodologies, change management, and project management initiatives, Core-Mark International’s Atlanta Division achieved an exceptional transformation. Strategic policies and guidelines, enhanced safety standards, and a culture of operational excellence propelled improvements in productivity, safety, and service levels. The Atlanta Division was recognized as “Best in Class” for multiple operational categories with in the Core-Mark network.
Endnote:
Continuous Improvement is a Journey, You Just Need the Right Guide…
-
From Red to Black: Breaking Through the Backlog of Inefficiency
Company: Hopkins Manufacturing Corporation
Backdrop:
Hopkins Manufacturing Corporation, a notable entity in the industry, faced a multitude of challenges in optimizing their Distribution Center (DC) operations and Supply Chain processes. Determined to overcome these obstacles and achieve operational excellence, they embarked on a transformative journey. Their aim was to elevate efficiency, improve key performance metrics, and realize significant outcomes through the rigorous implementation of Lean Six Sigma initiatives.
Pain Points:
Operational Inefficiencies: The absence of end-to-end Value Stream Mapping in DC operations and Supply Chain processes led to inefficiencies that hindered performance creating a backlog of over $5mm in sales.
Budget Management: Struggles in aligning with planned labor budgets impacted financial management.
Subpar or lacking Key Performance Indicators (KPIs): Challenges in enhancing or establishing critical KPIs such as CPH, Throughput, OTIF, Accuracy, Absolute Variance, Cost per Case, % to Sale, and Shrink.
Safety Incidents: Undesirable Safety Recordable Incident Rate underscored the urgency for safety improvements.
Lack of Process Control and Accountability: The absence of clear process control and accountability mechanisms contributed to operational challenges and a ownerless culture.
Strategic Solutions:
Value Stream Mapping: Comprehensive end-to-end mapping of DC operations and Supply Chain processes to identify and rectify inefficiencies.
Process Improvement: Design and implementation of Inventory Control (IC) processes leading to substantial cost recovery.
Lean Six Sigma Initiatives: Leadership in various initiatives including Transportation Cost Avoidance, Excess & Obsolete Inventory Reduction, and the implementation of a 5S program.
Ecommerce & Dropship Growth Strategy: Contribution to the design and execution of a growth strategy.
WMS Implementation: Steering committee membership and project leadership for Warehouse Management System (WMS) implementation.
3PL Business Partner Relationship Management: Oversight of performance and relationship management with 3PL partners.
Breakthrough Results:
Significant Improvement in KPIs: Notable improvements in CPH productivity and throughput.
- Improved CPH Productivity by 61.7 % 2019 – 2020, by 63.0% 2020 – 2021 & by 10.4% 2021 – 2022
- Improved Throughput by 75% 2020 – 2021 & 44.2% 2021 – 2022
Budget Alignment: Labor costs aligned with planned budgets for 2020 and 2021.
- 2020 Budget: Labor 94.1% in Line w/ Plan, 2021 Budget: Labor 97.3% in Line w/ Plan
Backorder Log Reduction: Reduced backorder log from $5MM to less than $500k in just 13 weeks.
Enhanced OTIF Performance: Substantial improvements in On Time In Full (OTIF) metrics over multiple years, reaching 99.5% on-time in 2022.
Improved Safety Recordable Incident Rate by 61.5% 2019 – 2020, by 60% 2021 – 2022 (2 Recordables)
Cost Savings and Avoidance: Implementation of Lean initiatives resulted in significant cost savings and avoidance across various projects.
- The E2E Supply Chain Lean Initiatives led to savings/cost avoidance of $1.43MM.
- The Transportation Cost Avoidance Initiative resulted in cost avoidance of $426K.
- The Inventory Reduction Initiative led to an E&O reduction of $3.8MM in addition to a rework savings of $1.52MM.
Recognition and Leadership Evolution:
The remarkable improvements in KPIs were reflected in the stellar performance of the operation. The successful integration of Lean Six Sigma initiatives pushed the operations to excel, and those involved saw their efforts rewarded with career advancement opportunities. The 5S Program earned the operation a “Best In Class” recognition.
Impressive Outcome:
Thanks to the robust application of Lean Six Sigma methodologies and a steadfast commitment to continuous improvement, Hopkins Manufacturing Corporation underwent a significant transformation. The journey from operational struggles to achieving remarkable improvements underscores the tangible benefits of Lean Six Sigma in overcoming challenges and delivering impressive results.
Endnote:
Continuous Improvement is a Journey, You Just Need the Right Guide…
-
Rising Above: From Bottom Ranks to Top Performance at Sam’s Club Super Center
Company: Saddle Creek Logistic Services
Backdrop:
Saddle Creek Logistics Services, operating as a Sam’s Club Super Center, faced a myriad of challenges in its 3PL environment. Despite being one of the highest volume distribution centers (DCs) in the Sam’s Club network, we found ourselves ranked second to last, 17th out of 18, in operational efficiencies. Needless to say, our business partner Walmart Inc. was not happy with the relationship. Driven by a relentless pursuit of excellence, we embarked on a transformative journey to enhance operational efficiency, elevate customer service standards, and achieve remarkable outcomes through the robust implementation of Lean Six Sigma and Continuous Improvement (CI) initiatives.
Pain Points:
Insufficient Training and Support: Lean Six Sigma training and mentorship for Green and Black Belts were lacking, demanding a structured training program to empower employees.
Customer Service Deficiencies: Service standards fell short, necessitating superior customer service and strengthened customer relationships, particularly critical in serving Sam’s Club.
Operational Inefficiencies: Inefficient space utilization in the yard and warehouse, suboptimal loading/unloading processes, and inadequate maintenance and sanitation practices posed significant challenges in a high-volume environment.
Financial Performance Scrutiny: Fiscal performance came under scrutiny, requiring effective management of profit & loss and budgeting to meet the demands of a Super Center.
Strategic Solutions:
Lean Six Sigma Training: Comprehensive Lean Six Sigma and CI training programs were facilitated for the Saddle Creek team, customer network, and leadership group to foster a culture of excellence, vital in a high-volume 3PL environment.
Quality Communication Initiative: Collaboration with customers and third-party carriers led to the design of a Quality Communication Initiative to enhance visibility and foster proactive and timely communication, especially critical in serving Sam’s Club.
Operational Excellence Program: An Operational Excellence Program was designed, implemented, and managed, encompassing multiple A3/CI initiatives to champion best practices in 5S, visual management, and process standardization, tailored to the demands of a Super Center.
Space Utilization and Service Level Enhancement: Optimization projects were executed to maximize yard and warehouse space utilization efficiency, manage inbound and outbound loading/unloading processes, and ensure high service levels to meet the demands of Sam’s Club.
Breakthrough Results:
Exceptional Training Outcomes: Lean Six Sigma training resulted in proficient Green and Black Belts, fostering a culture of operational excellence crucial in serving Sam’s Club as a Super Center.
Customer Service Boost: The Quality Communication Initiative improved customer relationships and overall service quality, enhancing the partnership with Sam’s Club.
Operational Improvements: The Operational Excellence Program saw a Corporate Safety Audit score of 98 – the “best score in the company,” as stated by the Corporate Safety Team Leader. Yard space optimization leading to annual savings of over $130k+ and a significant 54.2% improvement in carrier cycle time and the Warehouse Space Optimization Project increased productivity by 7.7%.
Service Level Excellence: Live Appointments soared to 99.89%, while Drop Appointments reached 99.9%, ensuring prompt and efficient operations, meeting the high standards set by Sam’s Club.
Fiscal Performance Enhancement: Notable cost savings were realized, with Total Equipment R&M/Misc Expense decreasing to 55.47% compared to plan – Q1 FY20, and Total Facility Expense falling to 91.2% compared to plan – Q1 FY20, aligning with the financial expectations of a Super Center.
Recognition and Leadership Evolution:
The significant improvements at Saddle Creek were reflected in elevated operational and safety scores, critical in serving Sam’s Club. The successful adoption of Lean Six Sigma culture propelled operations beyond expectations, offering employees rewarding career growth opportunities.
Impressive Outcome:
Thanks to the diligent application of Lean Six Sigma methodologies and a strong commitment to continuous improvement, Saddle Creek Logistics Services underwent a remarkable transformation. From ranking second to last to securing the number one position in operational efficiencies within just one year, the journey underscores the tangible benefits of Lean Six Sigma and Continuous Improvement initiatives, particularly in a high-volume 3PL environment serving Sam’s Club as a Super Center.
Endnote:
Continuous Improvement is a Journey, You Just Need the Right Guide…
-
Makin’ Bacon: The Journey to a Record-Breaking year in EBITDA
Company: Daily’s Premium Meats
Backdrop:
Daily’s Premium Meats, known for its delectable bacon, faced formidable challenges within their manufacturing facilities. With limited KPIs in place to measure operational efficiency and escalating costs, the company sought to revolutionize its operations and achieve unprecedented success. The focus was on setting standards for process control and records for EBITDA. However, the path to excellence was paved with many obstacles.
Pain Points:
Limited Operational Metrics: The absence of comprehensive KPIs hindered the ability to measure consistent operational efficiencies throughout the operations departments.
Regulatory Compliance: Struggling to align with stringent USDA regulations added complexity to operations and posed compliance challenges.
Yield Optimization: Suboptimal yield rates led to significant waste and operational inefficiencies, impacting profitability.
Equipment Capacity: Insufficient equipment capacity limited production output and hindered scalability.
Warehouse Inefficiencies: Inefficient warehouse operations contributed to delays and disruptions in the supply chain, affecting overall productivity.
Strategic Solutions:
Comprehensive KPI Definition: Collaborate with stakeholders to define and implement a robust set of KPIs, including Conversion Costs, Downtime, PONC, Schedule Adherence and more, to accurately measure operational performance.
Operational Excellence: Partner with Quality Assurance and Talent Development departments to design and centralize company standards and best practices. Design & implement a comprehensive Process Controls Audit Program to monitor and regulate process compliance and efficiency.
Line Standardization: Implement process standardization and 5S practices in the Food Service & Retail Departments.
Warehouse Operations Optimization: Develop strategies to address warehouse inefficiencies, including implementing standard work practices and a 5S Program, targeted to improve inventory accuracy, fill rate, and OT reduction.
Breakthrough Results:
Record-Breaking EBITDA: Achieved a record year for EBITDA in 2022, setting new standards for profitability and financial performance.
Published over 240 Process Standardization Documents, ensuring consistency and efficiency across operations.
Achieved remarkable improvements in PPMH (+61.7%), Yield (+2.08%), Capacity Utilization (+13.1%), Downtime Reduction (-5.3%), Giveaway Reduction (-1.8%), and Defect Reduction (-5.2%).
Oven Capacity – Increased output at the Utah Plant, yielding an incremental annualized benefit of $1.4 million.
Identified and addressed opportunities to reduce shrinkage, resulting in annual cost savings of $570,000 at the MO Plant.
Optimize warehouse operations, resulting in significant improvements in inventory accuracy (+29.4%), fill rate (+12.3%), and OT reduction (-10.6%).
Impressive Outcome:
Through strategic initiatives and a relentless commitment to excellence, Daily’s Premium Meats transformed its manufacturing plant into a beacon of operational excellence and profitability. By addressing key pain points, setting new standards for performance, and embracing continuous improvement, the company has solidified its position as a leader in the bacon production industry.
Endnote:
Continuous Improvement is a Journey, You Just Need the Right Guide…