In today’s competitive business landscape, efficiency isn’t just an advantage—it’s a necessity. Companies continuously strive to optimize their operations, reduce waste, and boost productivity. One proven approach to achieving these goals is through business process improvement consulting. By partnering with a skilled business process improvement consultant, organizations can streamline their operations, uncover hidden inefficiencies, and foster a culture of continuous improvement.
For an insightful introduction to how these strategies can transform your operations, watch this video: Watch Video
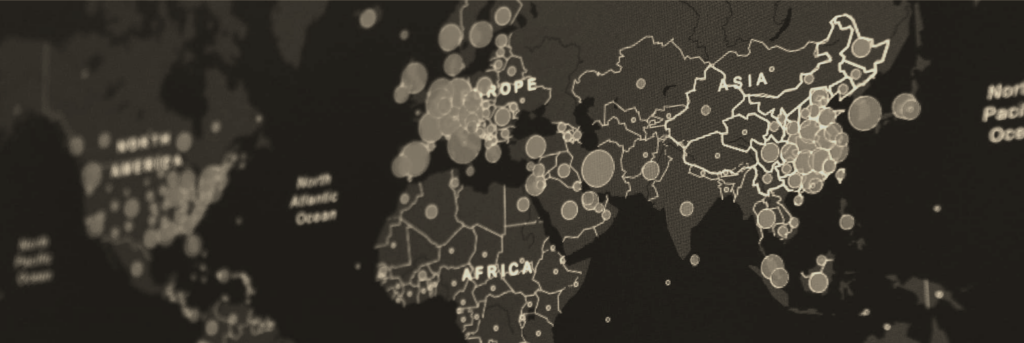
What Is Business Process Improvement Consulting?
Business process improvement consulting involves a systematic approach to helping organizations analyze, design, and implement better business processes. Consultants in this field utilize proven methodologies, such as Lean Six Sigma, to identify inefficiencies, eliminate waste, and optimize workflows. The goal is to create streamlined, agile processes that enhance overall business performance and drive sustainable growth.
Through business consulting services, experts work alongside organizations to:
- Map existing processes in detail.
- Identify bottlenecks and redundant steps.
- Develop strategies to eliminate inefficiencies.
- Implement solutions that improve quality, speed, and cost-effectiveness.
The Critical Role of a Business Process Improvement Consultant
A dedicated business process improvement consultant serves as both a guide and a catalyst for change within an organization. Here’s how these professionals make a difference:
1. Diagnostic Expertise
The first step in any process improvement initiative is understanding the current state of operations. A seasoned consultant conducts comprehensive assessments, employing techniques such as process mapping, root cause analysis, and performance benchmarking. This diagnostic phase reveals hidden inefficiencies, pinpointing exactly where improvements can yield the greatest impact.
2. Strategy Development
After identifying key areas for improvement, the consultant collaborates with stakeholders to develop a tailored strategy. This often involves leveraging Lean Six Sigma methodologies to set measurable goals and define clear, actionable steps. By establishing data-driven targets, organizations can track progress and ensure that improvement initiatives align with overall business objectives.
3. Implementation and Change Management
Implementing process improvements requires careful planning and robust change management. A business process improvement consultant guides the organization through this transition, ensuring that new processes are smoothly integrated into the existing framework. They work closely with teams to provide training, adjust workflows, and manage any resistance to change, ensuring that improvements are sustainable in the long term.
4. Continuous Monitoring and Optimization
The work of a consultant doesn’t stop once a new process is in place. Ongoing monitoring and periodic reviews are essential to ensure that the improvements continue to deliver the desired results. Regular performance assessments and feedback loops allow for continual refinement and adjustment, keeping the organization agile and competitive.
Leveraging Business Process Consulting Services for Operational Excellence
Comprehensive business process consulting services offer end-to-end support that spans from initial analysis to full-scale implementation. These services typically include:
- Process Audits: A thorough review of current processes to identify strengths, weaknesses, and opportunities for improvement.
- Workflow Optimization: Redesigning workflows to reduce redundancy and increase efficiency.
- Performance Metrics: Establishing key performance indicators (KPIs) to measure the success of improvement initiatives.
- Technology Integration: Implementing software and automation tools that streamline operations and facilitate data-driven decision making.
- Training and Support: Providing the necessary training and support to ensure that all team members understand and adopt new processes effectively.
By engaging in business process improvement consulting, companies can not only boost their operational performance but also gain a significant competitive edge in their industry.
The Lean Six Sigma Advantage
At the heart of many process improvement initiatives is Lean Six Sigma—a powerful methodology that combines the efficiency of Lean with the precision of Six Sigma. Lean Six Sigma focuses on reducing waste, enhancing quality, and improving overall process performance through a structured, data-driven approach.
Key benefits of incorporating Lean Six Sigma into your process improvement strategy include:
- Waste Reduction: Systematically eliminating non-value-added activities from your processes.
- Enhanced Quality: Using statistical tools to reduce variability and ensure consistent performance.
- Cost Savings: Streamlining operations leads to lower operational costs and increased profitability.
- Customer Satisfaction: Improved processes result in higher quality products and services, which boost customer satisfaction and loyalty.
By integrating Lean Six Sigma with business consulting strategies, your organization can drive significant operational improvements that deliver lasting value.
Implementing Process Improvements: A Step-by-Step Guide
Implementing business process improvements involves several key steps:
1. Initial Assessment
Begin by conducting a thorough audit of your current processes. Identify areas where inefficiencies exist and gather data to understand the impact of these issues on your overall operations.
2. Goal Setting
Define clear, measurable goals for your process improvement initiatives. Whether it’s reducing cycle times, lowering costs, or improving product quality, setting specific targets will guide your efforts and provide a basis for measuring success.
3. Process Mapping
Create detailed maps of your current workflows. Visualizing the processes helps to identify redundant steps and bottlenecks that hinder efficiency.
4. Analysis and Design
Using Lean Six Sigma tools, analyze the data to pinpoint the root causes of inefficiencies. Develop a redesigned process that eliminates waste, enhances quality, and streamlines operations.
5. Implementation
Roll out the new process in a structured manner. Ensure that all stakeholders are informed, trained, and supported during the transition.
6. Monitoring and Optimization
Establish KPIs and monitor the new process closely. Use regular feedback and performance data to make adjustments as needed, ensuring that the improvements are sustainable over time.
For a deeper dive into how these strategies can transform your operations, watch this video: Watch Video
Conclusion
In a competitive market, operational efficiency is a key driver of success. Business process improvement consulting offers a proven pathway to streamline operations, reduce waste, and enhance productivity. By partnering with a skilled business process improvement consultant, you can gain the insights and expertise needed to implement effective process improvements that drive measurable results.
Comprehensive business process consulting services, anchored by Lean Six Sigma methodologies, empower your organization to achieve operational excellence and sustainable growth. Embrace the power of process improvement to transform your business operations and secure a competitive advantage in today’s dynamic market.
Invest in your organization’s future by taking the first step toward streamlined, efficient, and effective operations.